Revolutionising conveyor operations: a case study on promet's starclean® scraper
In the relentless mining world, operational downtime translates to significant financial costs. Our client contacted us at Promet, hoping to achieve what seemed impossible: a full year of uninterrupted conveyor operation on a lifeline belt from the belt scrapers. This is a monumental feat like no other. At the heart of this success for our client's mine site is our groundbreaking STARCLEAN® conveyor belt scraper.
This innovative scraper is the first of its kind globally. It features a bespoke retractable setup explicitly tailored for the rigorous demands of handling the heavily abrasive material Magnetite. Learn how we installed the conveyor belt scraper with a promise of durability and how it has outperformed expectations, lasting an impressive year plus continuous operations. This article delves into the remarkable journey of this massive project, the innovative solutions we employed, and the significant impact on our client's mining operations.
The challenge:
In early 2023, our client faced formidable challenges with their operations, such as maintaining continuous operations of one of their conveyors for an entire year without interruption. The stakes were high—safety, efficiency, and no conveyor belt damage were paramount.
They were struggling with high levels of material carryback due to the heavily abrasive Magnetite and the lack of scraper efficiency in their conveyor belt operations. With at least four existing scrapers on this conveyor, the issue was no closer to being solved. During our initial stages of assessing our client's site through our auditing process, we found a collapsed return idler that became one of the many victims of the constant stream of fugitive material that damages the critical components essential for a conveyor's efficient and safe performance. Throughout our audit, we found and reported similar conditions across this conveyor system.
Primary Concerns:
During our audit of our clients' conveyors, we uncovered their primary concerns and challenges to clearly understand the vision and requirements they expected to achieve.
- The primary concern our client addressed was the quality of their conveyor belt scrapers; they were causing highly uneven wear, which exacerbated belt wear and damage. The resultant carryback caused considerable personnel safety issues in addition to all the regular problems carryback causes on a conveyor system.
- The challenge of our client's conveyor operations is the product we are dealing with, Magnetite, which is considered one of the more abrasive/hard material of its ranks; was leading to increased wear and tear on not only the scraper blades but also the conveyor belt and components.
- The constraints of their operations required continuous conveyor operation without much downtime, which meant the scrapers needed to be highly reliable, durable, and last the distance. A minimum mandate of 12 months lifetime was required.
Primary Goals:
Throughout our communication and auditing process with our client, we took the time to uncover and understand this project's primary goals.
- To achieve uninterrupted operation of this conveyor system for one whole year.
- Ensure safe operation without risking worker or belt damage.
- Maintain high belt cleaning efficiency.
- Minimising the maintenance requirements and downtime.
Our initial approach: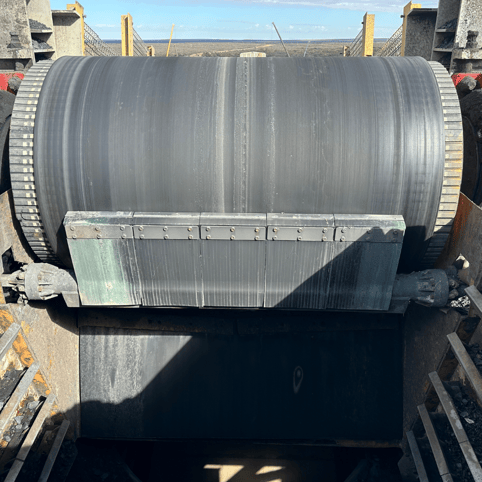
Once we had conducted our audit of our clients' conveyor system, we initially had a strategy that involved using our large series STARCLEAN® primary scraper with our 481 series polyurethane blades (the smallest of the large range). A normal series STARCLEAN® secondary scraper was also selected.
The primary scraper was selected for its safety profile, aiming to minimise the risk of operational mishaps. The mounting and tensioning system also required no maintenance for the blades' lifetime. As a proof of concept for the large scraper series, the scraper performed as expected in most aspects; however, it lacked the required lifetime to satisfy the target.
The crucial fact was that this scraper selection was correct, but we needed to select a different blade to provide the required lifetime. The magnetite with the high moisture content kept the scrapers honest!
- Durability: The polyurethane blades, though effective, were projected only to last four to six months, short of the one-year goal our client had in mind.
- Vibration Issues: Slip-stick friction caused slight vibration issues, exacerbated by the lack of moisture and product at each edge of the belt. A simple dash of water migrated the issue, allowing the blades to profile to the belt over time.
- Cleaning Effectiveness: Despite these challenges, the polyurethane blades on the STARCLEAN® scraper maintained exceptional cleaning effectiveness, outperforming previous scrapers our client had trialled.
Re-evaluation:
Recognising the limitations of the polyurethane blades for the life required, the only alternative while maintaining high cleaning efficiency was to use our heavy-duty Tungsten Carbide variant, which incidentally fits into the same scraper bar, and no other modifications are needed. Using a large PU blade is possible, and while lifetime improves, there is a potential effect on diminished cleaning performance. The TC variants are renowned for their incredible durability and effectiveness; this was the pivotal moment in the project.
It was also crucial that the scrapers could easily be accessed and maintained without significant downtime. This was not an easy feat for a considerably large setup, with service access not considered in the initial preparation stages; we overcame this with the recent and final upgrade of the tailor-made retractable system.
The solution:
After carefully considering all aspects of our clients' contractions, performance requirements and serviceability, we presented them with a one-of-a-kind, custom-designed STARCLEAN® Type 83RS-HD Conveyor Belt Scraper.
What benefits does this unique scraper bring to our client?
- The Extended Blade Life:
- The tungsten carbide blades demonstrated an impressive lifespan of over one year, with less than 10-15% wear.
- Significant improvements in durability, reducing the frequency of blade replacements.
- Quickly achieve the one-year minimum requirements our client desires.
- Operational Efficiency:
- This STARCLEAN® Conveyor belt scraper's design allows quick and easy blade maintenance.
- Retractable blade carrier enables replacement blade changes in less than 30 minutes.
- Switching the blade materials makes it adaptable to varying operational needs without compromising the cleaning performance.
- The innovative TWIST-SWING® function allows each scraper blade to adjust perfectly to the belt surface, resulting in flawless cleaning and the ability to evade obstacles without damaging the scraper blade or conveyor belt.
- Our scrapers' easy maintenance process reduces downtime by at least 80%.
- Maintenance and Reliability:
- Minimal maintenance requirements due to the robust design of the conveyor belt scrapers.
- Our scraper design provides tool-less blade replacement and easier access for maintenance, which means maintenance adjustments can be carried out with reduced downtime and effort.
- Various tensioning devices ensure the scraper blade maintains optimal pressure against the belt, enhancing its cleaning efficiency and blade life.
- Cost Savings:
- The extended blade life and reduced frequency of replacement blades have led to the client reducing maintenance costs, saving an estimated cost of roughly 70% annually. The durable tungsten carbide blades and the ability to quickly switch to polyurethane blades when necessary have minimised the operational costs for our client.
With great confidence in the superior quality of our tungsten blades, we proceeded with the upgrade for our client. The new blades were designed to withstand the harshest conditions and provide consistent, even wear, thereby avoiding the shortcomings of the previously tried conveyor belt scrapers.
Our STARCLEAN® conveyor belt scraper has proved to be an indispensable asset to our client's conveyor operations, delivering exceptional performance, durability, and client satisfaction. Its innovative design and robust construction significantly reduce maintenance downtime and operational costs while increasing the overall efficiency of the conveyor system.
Why choose promet?
Our services don't just stop there. We offer a comprehensive range of equipment and services to optimise conveyor performance. Our product range includes scrapers for all applications, modular plough scrapers, belt tracking systems, impact beds, transfer point seals, and more. All our products are engineered to meet the demanding needs of bulk material handling operations. We also provide expert consultation, auditing, installation and maintenance services to ensure your conveyor system operates efficiently.
So, if you're looking for reliable and efficient conveyor belt cleaning solutions or need support with any aspect of your system, our suite of conveyor optimisation solutions is your answer!
Contact us today to learn more about how we can help optimise your operations and keep your conveyor systems running smoothly.